Materials
Where to start? Choose your material
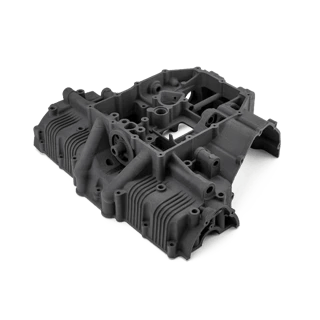
The best 3D Printing material for cost-effective production. Most wanted for MJF manufacturing and largely employed by businesses for prototyping and long runs.
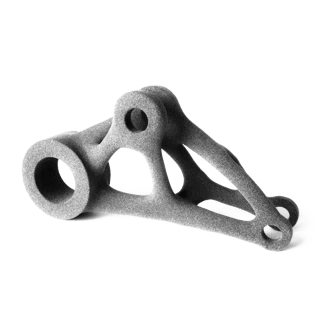
More flexible and impact resistant than PA12 and more eco-friendly. In addition, its resistance to many chemicals results in excellent wear and abrasion resistance and it has low friction properties.
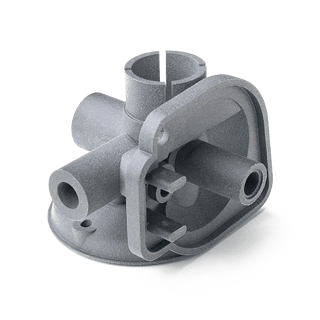
The Nylon PA12 GB is added 40% with glass beads to improve stiffness and resistance to wear and heat resistance. Perfect for automotive, industrial, and consumer applications.
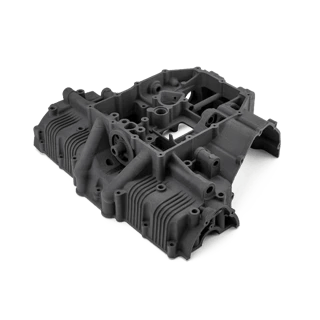
Available colors:
The best 3D Printing material for cost-effective production. Most wanted for MJF manufacturing and largely employed by businesses for prototyping and long runs.
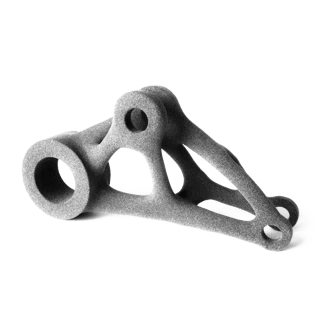
Available colors:
More flexible and impact resistant than PA12 and more eco-friendly. In addition, its resistance to many chemicals results in excellent wear and abrasion resistance and it has low friction properties.
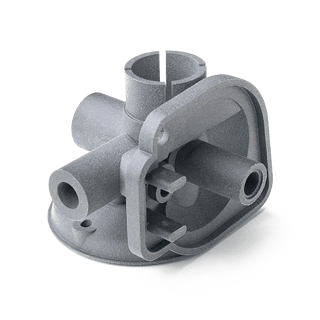
Available colors:
The Nylon PA12 GB is added 40% with glass beads to improve stiffness and resistance to wear and heat resistance. Perfect for automotive, industrial, and consumer applications.
Which one is the best 3D Printing material?
In 3D printing, material choice is crucial to achieve optimal results in terms of strength, flexibility and overall performance. The three best materials used in this technology are Nylon PA12, Nylon PA11, and Nylon PA12 with glass beads (GB). Each of these has unique characteristics that make them suitable for different applications. We will compare the key properties of these materials to help you make informed decisions on selecting the best material for your needs.
Tensile breaking load
Nylon PA12 | 52 MPa |
Nylon PA11 | 54 MPa |
Nylon PA12 GB | 31 MPa |
Tensile breaking load indicates the maximum limit of applied external force beyond which a material loses its functional specifications in terms of strength. Nylon PA11 shows the highest value in this category, followed by Nylon PA12 and Nylon PA12 GB.
Modulus of elasticity
Nylon PA12 | 2 GPa |
Nylon PA11 | 1.7 GPa |
Nylon PA12 GB | 2.9 GPa |
The modulus of elasticity represents the stiffness of the material. Nylon PA12 GB has the highest value, while Nylon PA11 has the lowest value among the three materials.
Elongation at break
Nylon PA12 | 15% |
Nylon PA11 | 39% |
Nylon PA12 GB | 7% |
Elongation at break measures the ability of a material to deform before breaking. Nylon PA11 demonstrates considerable flexibility, while Nylon PA12 GB has significantly lower elongation at break.
Flexural modulus
Nylon PA12 | 1730 MPa |
Nylon PA11 | 1400 MPa |
Nylon PA12 GB | 2400 MPa |
Flexural modulus indicates the material's resistance to bending. Here, Nylon PA12 GB is the strongest material, followed by Nylon PA12 and PA11.
HDT (Heat Deflection Temperature) at 0.45 MPa
Nylon PA12 | 175°C |
Nylon PA11 | 175°C |
Nylon PA12 GB | 171°C |
HDT represents the temperature at which a material begins to deform under thermal load. Nylon PA11 has the highest value, indicating good resistance to high temperatures.
Izod impact resistance
Nylon PA12 | 3,5 kJ/m² |
Nylon PA11 | 7 kJ/m² |
Nylon PA12 GB | 3,6 kJ/m² |
Impact resistance measures the material's capacity to absorb energy and deform plastically without fracturing. The Izod test is carried out by releasing a pendulum from a height and causing it to impact the material specimen, so as to bring it to fracture. The energy absorbed by the specimen during impact is calculated from the maximum height the pendulum reaches after impact. Nylon PA11 shows significantly higher impact resistance than the other two materials.
Tolerances
Nylon PA12 | ±0.01 in < 3.94 in ; ±0.3% > 3.94 in |
Nylon PA11 | ±0.02 in < 3.94 in ; ±0.5% > 3.94 in |
Nylon PA12 GB | ±0.01 in < 3.94 in ; ±0.3% > 3.94 in |
Maximum size
Nylon PA12 | 15 x 11.2 x 15 in |
Nylon PA11 | 15 x 11.2 x 15 in |
Nylon PA12 GB | 15 x 11.2 x 15 in |
The maximum print size is identical for all three materials, allowing the production of generously sized parts.
In conclusion, the choice of material depends on the specific requirements of the project. Nylon PA11 tends to be used for mechanically loaded functional prototypes, automotive interior components, long-term mobile production (such as zippers) and mass-produced parts. Conversely, Nylon PA12 stands out for its versatility at a low cost. Therefore, it is a combination of strength, durability, abrasion and chemical resistance, and dimensional stability. Finally, Nylon PA12 GB offers outstanding mechanical performance making it ideal for gaskets, items requiring uniform sliding action and parts for large industrial applications.